Engineering researchers ensure tools and electronic devices function smoothly
Words like tribology and hydrophobicity mean little to most people, yet research in these areas – the study of friction, wear, and lubrication and the ability of a substance to repel water, respectively – improve the tools we use every day.
And University of Arkansas mechanical engineering professor Min Zou is recognized as an international expert in both fields. She specializes in using nanomaterials to texturize surfaces of commercial products and electro-mechanical systems to reduce friction and improve energy efficiency. Her work is contributing to improvements in everything from electronic devices to tissue engineering and even everyday kitchen skillets.
“Polytetrafluoroethylene is a big, scary word,” Zou said, explaining the technical name for the polymer commonly known as Teflon. “It’s simply a material layer or coating – we call it a film – that essentially does not stick and is hydrophobic, meaning it repels water. Our goal is to make it even more water repellent.”
Zou led a team of researchers who discovered a way to do exactly that, to make Teflon even more slippery. They treated thin films of the polymer with copper nanoparticles and found that the lubricating material significantly reduced both wear and friction.
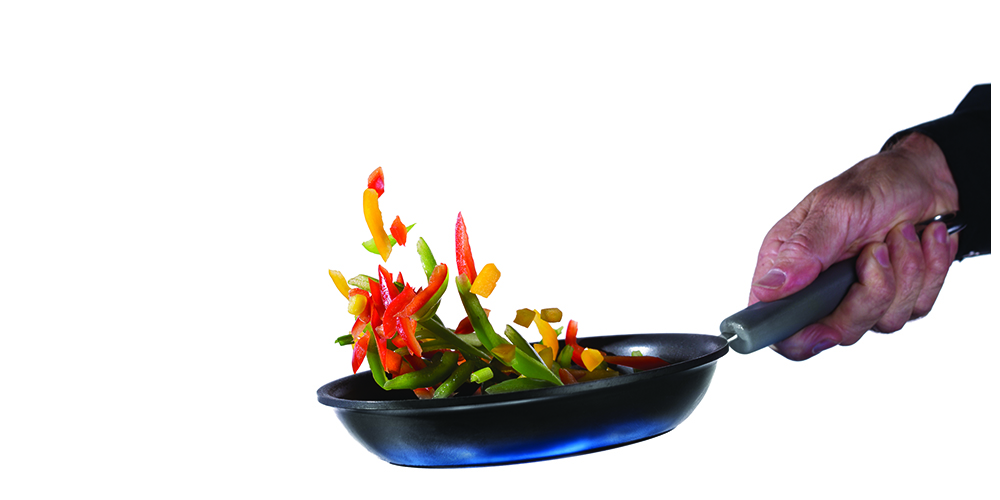
These core-shell nanostructures can be incorporated into solid surfaces where mechanical integrity of nanostructures is vital. They consist of a metallic core covered by a hard shell made of various nano-scale material. It holds its shape after being subjected to extremely high friction.
Zou also leads a multi-institutional, interdisciplinary team that received a $20 million grant from the National Science Foundation to create a statewide Center for Advanced Surface Engineering. This grant enables the University of Arkansas to partner with industries and create new products for manufacturing, aerospace, defense, agriculture, oil and gas, food packaging and healthcare. The center will include four interdisciplinary research teams and integrate industry partners into the curriculum through internships and seminars.
As part of the NSF’s Experimental Program to Stimulate Competitive Research — EPSCoR — which promotes scientific progress nationwide through partnerships across the public and private sectors, the center will establish start-up companies to commercialize technologies developed by its researchers and create new products and jobs.
One such company, WattGlass, is working to commercialize anti-reflective, self-cleaning coatings for solar panels and other glass applications that were developed by Zou and two graduate students during previous EPSCoR-funded research.
The coatings spread water rapidly across glass, creating a surface that is both self-cleaning and anti-fogging as water doesn’t bead up. The coatings also reduce reflection from the glass, making solar cells more efficient.
WattGlass has received more than $1 million in grants from NSF and the U.S. Department of Energy to further develop these nano-particle coatings for large-scale projects using commercial coating equipment. “Micro- and nano-electro-mechanical systems hold great promise to revolutionize nearly every product category, from computer hard drives to automotive and biomedical devices,” Zou said.